Forged Monoblock Alloy Wheel - Just A Better Wheel
PPE Wheel Product Lines
Your choice for luxury and performance with the most details and flexibility for customization. Featuring high performance and high-end style in engineering details, size available from 18 to 22 inch, each wheel is order to make to suit your personal application.
Choice of "Extreme" option for all the details of the rear
Signature by its "Star" pattern from the front face, weight saving pockets has bring from back to front to form this distinctive star shaped pattern for the enthusiastic who focus in high performance for road and track. Available from 17 to 22 inch.
Choice of "Extreme" option for all the details of the rear
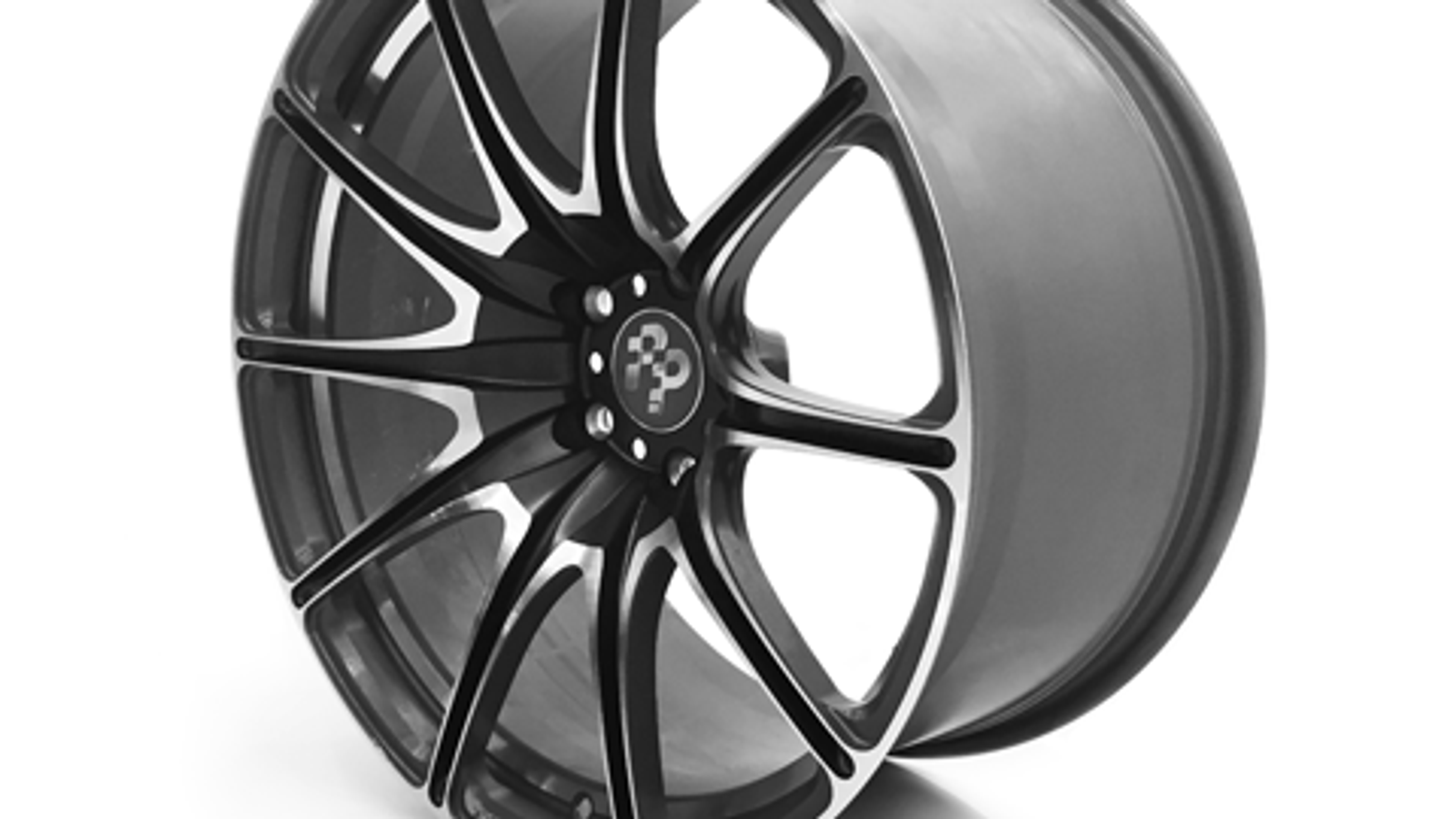
PPE Wheels Details
Engineering Design Methodology
PPE manufactures forged monoblock alloy wheels, which is the strongest and lightest weight in its class, and manufactured by using a true forging process with high precision CNC machining. All PPE forged wheels complies with a safety and engineering standard called PWS (ProPioneer Engineering Wheel Specification) which is higher than commonly used standards such as VIA or DOT. To understand more about wheels manufacturing process, you can follow here. To learn more details about the PWS, please click here.
Each PPE forged wheel is an engineering masterpiece. designed and engineered with integration of styles and mechanical strength, not just to meet minimum common road wheels standards such as VIA and TUV specifications. In fact, we use a higher proprietary specification to design our wheels known as PWS (ProPioneer Wheel Specifications) to suit modern high performance vehicles and racing applications. This is achieved by using a higher safety factor, higher rated load. We also take into account of torsional stress which is critical in tuned high power vehicles, and extreme high performance braking scenarios.
With our decades of experience in motorsports and tuning, we understand the importance of any single gram of unsprung weight affects to vehicle handling and performance . From the beginning, we have carefully design our wheel patterns to optimize balance of weight and strength for high performance vehicles. not just the front face outlook, also the side and rear of spokes, taking care engineering design details in all directions.
All wheels are precisely made using state of the art CNC machining and treatments. Resulting with a roundness precision of close to thousandth of an inch (0.001").
Design Process and Features
Advanced Computer Simulation Technologies
To optimize the engineering designs of our wheels, extensive use of advanced computer simulation known as finite element analysis (FEA) is performed to achieve the best strength to weight ratio with application specific rated load. This enables the achievement of minimized unsprung mass and rotational inertia to maximum strength and stiffness.
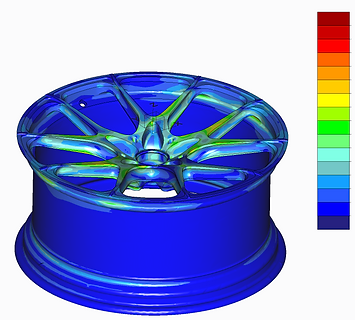
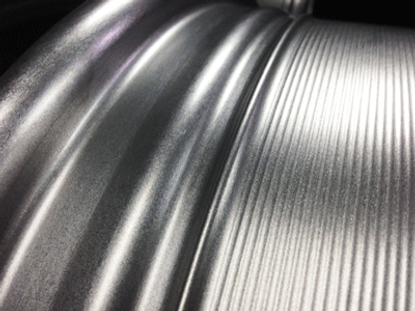
Reinforced Rim Barrels
Experiences told us under certain high speed scenarios, a thin rim barrel causes harmonic vibration, results in run-outs of the circular rim. Additional reinforcement ribs is added to the inner rim barrel to increase its circular stiffness to deal with these requirements.
Double Ribbed Barrel
Extra rib is added in the inner lip (wheel barrel) to improve stiffness and maintain roundness of the wheel. This not just gives better handling and response, also holds a better roundness tolerance.
Reinforced Inner Lips
With the increasing power and weight of luxury vehicles, we have introduced a inner lip (brake side) reinforcement option, it gives more strength of the inner lip resist against speed bumps and road hazards for heavy vehicles.
This is an option for users who intend to use their vehicle in rough road conditions.
Recommended for cars that has a gross weight of 2 tonnes above and with low profile tires.

Standard Design

Reinforced Design
To learn more about PPE wheels manufacturing process, please click here.