Forged Wheels - How It's Made
Manufacturing Process
Forging
Starting with an aerospace-grade aluminum round billet, and stamp forged using thousands of tonnes of pressure with suitable forging dies to transform the aluminum alloy to form a compact grain structure. This process ensures the elimination of material defects such as micro cracks and potholes within the solid.
Spun Forge / Flow Forming
The rim of the wheel is formed into a thin wall structure by high pressure spinning over a special mandrel. Hydraulic rollers roll against the mandrel and creating the shape and desired width of the rim. This even further compacts the material grain structure to form a high strength rim barrel


Heat Treatment / Aging
These forged and spun wheels rough blanks will take to an oven for heat treatment known as tempering, forming a black solid. This is to further improve their material properties such as strength, hardness and endurance limits, and increase the resistance of deformation.
PPE Wheels CNC Work
PPE Wheels CNC Work


PPE Wheel Blank Turning
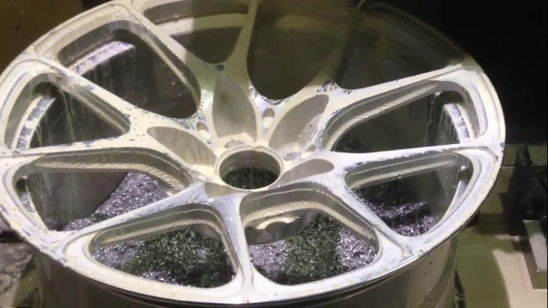
PPE Track Star V10 Front Milling

V10 Extreme Rear Milling
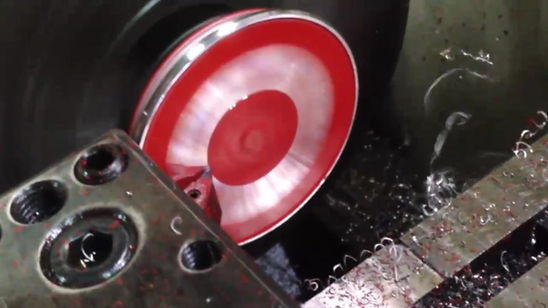
PPE Wheel Cap Diamond Cut
CNC Turning
The heat-treated wheel blanks are CNC turned to form a round and smooth surface, forming a profiled blank. The wheel profile of the blank is machined according to customer-specific requirements, such as specific concave or flat pattern, and designated offset/ET face.
Front CNC Milling
The turned blank wheels are sent to CNC milling centers to cut out the front face patterns, windows, and spokes. this process can take days to complete, depends on the pattern of the wheel.
Back CNC Milling
A unique process developed by PPE. To achieve an extra weight saving of the wheel on some specific models, such as the “Extreme” series, a patent-pending proprietary engineering process is done on the back of the wheel forming a distinctive 3D star shape weight saving pockets.
Spoke Side CNC Milling
On some specific “Extreme” series, an advanced machining process developed by PPE using multi-Axis CNC Technology with proprietary tooling, forming an I-beam cross-section that maximize strength and stiffness using least weight contribution.
Stress Relief, Sharp Edge Removal, and Final Finishing
All PPE Wheels goes through a unique process that relief all stresses, removal of gails and sharp edges through a proprietary automated peening and polishing process. this process not just relieves all the tensile stress generated during machining, it also relieves all the internal stresses during the forging process thus improved fatigue strength (longer life) of the wheel. Since this process is done after all the major machining work, the resulting wheel after this process is a very stable object with no further mechanical distortion possibilities. The wheel is then sent to the final fine turning for absolute perfect roundness and hub centricity.
Shot Blasting/Peening
To extend and improve wheels' fatigue strength, all wheels go through a blasting and peening process. This is a very important process for the wheels stresses fatigue life cycle.
Powder Coating / Painting
All wheels are coated with special formulated powders, colored coatings, and clear coatings. The powders are a type of polymer that bakes onto the wheel surfaces designed to form a hard surface with long life.



Spokes Highlight/Diamond Cut
Spokes CNC highlighting, diamond cut, track star pattern highlightings, all these processes are done after base powder coat, leaving all the machined areas in raw shiny aluminum.
Please click here to find out more about PPE wheels product line.